Introduction
In industries where extreme temperatures are the norm, the choice of materials used in manufacturing and construction is critical. High-temperature casting materials, also known as refractory materials, play a vital role in ensuring the efficiency, durability, and safety of heat-intensive operations. From metal casting and cement production to power plants and petrochemical industries, refractory materials are the unsung heroes that withstand intense heat, corrosion, and mechanical stress.
At Wilest Energy Solutions, we specialize in providing top-quality refractory materials that enhance performance and longevity in high-temperature environments. Whether you need solutions for furnaces, kilns, boilers, or foundries, our advanced refractory materials are designed to deliver superior heat resistance and durability.
What Are Refractory Materials?
Refractory materials are heat-resistant substances that can withstand extreme temperatures without degrading or losing their structural integrity. They are primarily used to line furnaces, incinerators, reactors, and other industrial equipment exposed to high heat, pressure, and corrosive elements.
These materials are engineered to maintain their strength even under thermal cycling, making them essential for industries that require continuous high-temperature operations.
Types of High-Temperature Casting Materials
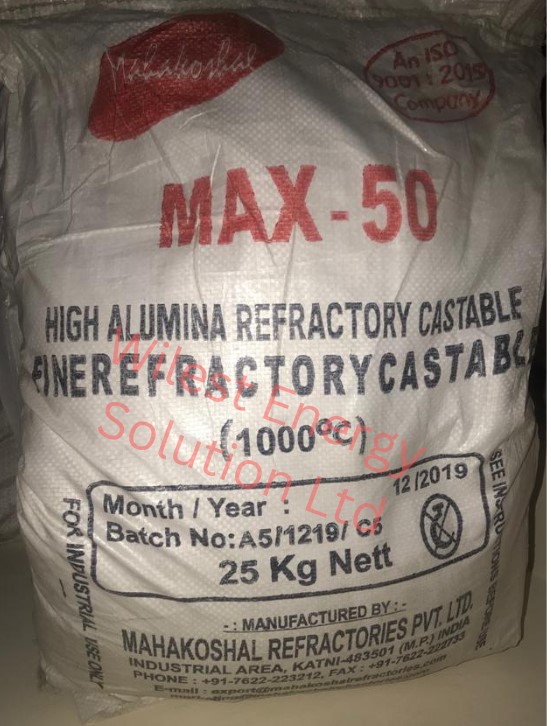
Refractory materials come in different compositions, each tailored for specific applications. Some of the most commonly used high-temperature casting materials include:
1. Fireclay Refractories
- Made from aluminum silicate
- Excellent resistance to heat up to 1,500°C
- Commonly used in boilers, kilns, and chimneys
2. High-Alumina Refractories
- Contain more than 45% alumina (Al₂O₃)
- Withstand temperatures of up to 1,800°C
- Used in steel-making furnaces, cement kilns, and incinerators
3. Silica Refractories
- Composed of more than 93% silica (SiO₂)
- High resistance to thermal shock
- Ideal for glass melting furnaces and coke ovens
4. Magnesia Refractories
- High magnesium oxide (MgO) content
- Exceptional resistance to alkaline slags and high heat
- Perfect for steel furnaces, cement kilns, and non-ferrous metal industries
5. Castable Refractories
- Easily shaped and applied on-site
- Used for lining furnaces, boilers, and incinerators
- Withstand temperatures above 1,700°C
6. Insulating Refractories
- Lightweight materials designed for thermal insulation
- Help reduce heat loss and energy consumption
- Used in kiln linings, furnaces, and foundries
Why High-Temperature Casting Materials Are Essential
Industries that deal with high temperatures require materials that offer reliability, efficiency, and safety. Here’s why refractory materials are indispensable:
✅ Heat Resistance – Protects industrial equipment from extreme temperatures.✅ Corrosion & Chemical Resistance – Prevents damage from molten metals, slags, and gases.✅ Thermal Shock Resistance – Withstands rapid temperature fluctuations.✅ Energy Efficiency – Helps retain heat and reduce fuel consumption.✅ Durability & Longevity – Extends the life of furnaces and industrial structures.
Applications of High-Temperature Refractory Materials
Refractory materials are used across various industries, including:
Metallurgy – Lining for blast furnaces, ladles, and smelting crucibles.Cement & Lime Kilns – Protection against extreme heat and abrasion.Power Plants – Boiler linings for coal-fired and biomass energy plants.Petrochemical Industry – Furnace and reactor linings for refineries.Glass & Ceramics – High-purity refractories for glass melting furnaces.
Wilest Energy Solutions: Your Trusted Partner in Refractory Solutions
At Wilest Energy Solutions, we supply premium refractory materials tailored to meet the demands of high-temperature applications. Our solutions are:
🔹 High-Performance – Engineered to withstand extreme heat and pressure.🔹 Energy Efficient – Reduce heat loss and optimize fuel consumption.🔹 Customizable – Available in different shapes and compositions for diverse applications.🔹 Cost-Effective – Durable materials that minimize downtime and maintenance costs.
Conclusion
High-temperature casting materials (refractory materials) are a critical component in heat-intensive industries, ensuring that furnaces, kilns, and boilers operate efficiently and safely. Investing in high-quality refractories enhances performance, reduces operational costs, and extends the lifespan of industrial equipment.
Looking for reliable refractory solutions? Contact Wilest Energy Solutions today and let us help you choose the right materials for your needs!
Call/WhatsApp: +254 707 346 616Visit: wilestboilersandinsulation.com
Wilest Energy Solutions – The Future of Energy & Industrial Innovation!